Elektronik 03/2014 - Szybkie i efektywne metody testowania pokryć zabezpieczających płytki drukowane
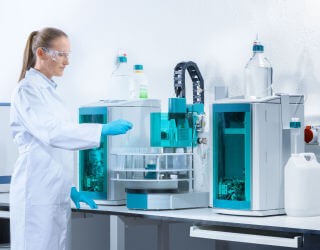
Jak test niezawodności powłoki ochronnej może przyśpieszyć pracę nad nowym projektem wyrobów elektronicznych i zapobiec kosztownemu przeprojektowywaniu gotowego urządzenia? Tego można dowiedzieć się z poniższego artykułu.
Szybkie i efektywne metody testowania pokryć zabezpieczających płytki drukowane
W trakcie projektowania urządzeń elektronicznych konieczne jest przeprowadzanie badań powłok ochronnych, co pozwala uniknąć kosztownego przeprojektowywania w późniejszym czasie po wykryciu błędów na koniec pracy nad projektem. Niestety większość z dostępnych metod pomiarowych jest czasochłonna i kosztowna. Poniższy artykuł prezentuje szybsze i tańsze sposoby, które są wystarczające do jednoznacznej oceny jakości i wytrzymałości powłoki zabezpieczającej.
W ostatnim czasie można zaobserwować duży wzrost znaczenia elektroniki we wszystkich rodzajach wyrobów. Mówiąc na przykład o branży motoryzacyjnej, można szacować, że około 30% wartości samochodu stanowią komponenty elektroniczne. Ten dynamiczny wzrost zwiększa obawy o niezawodność w niektórych warunkach środowiskowych, bo producenci aut używają identycznych komponentów do produkcji zarówno dla rynku europejskiego, jak i w rejonach, gdzie panuje klimat tropikalny. Taka sama niezawodność musi być zagwarantowana w każdych warunkach.
Powłoki ochronne
Działanie agresywnego środowiska powoduje naprężenia, które nie tylko zagrażają temu konkretnemu elementowi, ale mają wpływ na niezawodność całego urządzenia. Najczęstsze problemy wywołane w ten sposób to elektromechaniczna migracja jonów, korozja, upływ prądu oraz zwarcia.
Prawidłowo dobrana i nałożona powłoka ochronna może być odpowiednim rozwiązaniem zapobiegawczym, które będzie zapobiegać tym uszkodzeniom i będzie gwarantować niezawodne użytkowanie bez względu na warunki otoczenia. Ważnym elementem w przypadku tworzenia takich urządzeń stał się sposób testowania pokrycia na etapie tworzenia produktu, tak aby wyeliminować kosztowne przeprojektowywanie i naprawy.
Szybka i efektywna metoda badania powłok ochronnych została opracowana przez jednego z czołowych producentów elektroniki kolejowej, wspólnie z firmą Zestron. Celem było znalezienie sposobu pozwalającego na określenie odporności klimatycznej w trakcie projektowania urządzenia i zapewnienie niezawodności działania urządzenia w 30-letnim okresie eksploatacji, obejmującym średni dzienny czas pracy 16 godzin w zakresie temperatur od -40 do 85 ᵒC i pełną ekspozycje na środowisko.
Metody testowania
Celem prac było znalezienie właściwej metody ochrony obwodów drukowanych przed wpływem środowiska. Sprawdzane były właściwości powłoki takie, jak przepuszczalność, wytrzymałość elektryczna oraz adhezja. Zabezpieczona płytka elektroniczna urządzenia stosowanego w kolejnictwie została poddana wymyślonemu przez firmę Zestron testowi niezawodności powłok ochronnych (Coating Reliability Test – CoRe Test). Bazuje on na odporności urządzenia na wodę i jest testem analizy słabości, a nie badaniem cyklu życia. Pozwala na uzyskanie szybkiej informacji na temat jakości i odporności powłoki ochronnej. Ten szybki test został specjalnie opracowany z myślą o projektowaniu urządzenia i nie zastępuje testu cyklu życia takiego urządzania. Test CoRe wykazuje jednak kilka zalet w stosunku do testu cyklu życia, które zostały zaprezentowane w tabeli 1 (tabela dostępna w pliku PDF).
Test CoRe jest używany jako test „najgorszego przypadku” i zapewnia, że wszystkie źródła problemów zostaną wskazane. Następnie wszystkie słabe punkty mogą zostać przeanalizowane pod względem ich znaczenia dla odporności względem rzeczywistych warunków otoczenia, jakie mogą wystąpić w trakcie eksploatacji urządzenia. Połączenie testu CoRe z testem żywotności urządzenia skraca czas rozwoju produktu i zapewnia, że żaden aspekt aplikacji nie zostanie pominięty.
Sposób wykonywania testu
Test niezawodności pokryć CoRe wymaga, aby płytka elektroniczna została włożona do wody dejonizowanej lub wody dejonizowanej z dodatkiem 5% siarczku amonu. Następnie urządzenie jest zasilane w taki sposób, w jakim ma rzeczywiście pracować (np. 24 V). płynący prąd pracy jest mierzony, a następnie rysowany na wykresie funkcji czasu, aby sprawdzić występowanie elektrochemicznej migracji oznaczającej awarię. Złącza zostały wstępnie pokryte woskiem, aby osłonić je przed wodą. Poza analizą wykresu zmienności prądu w funkcji czasu, płytka jest także sprawdzana wizualnie pod kątem korozji i występowania elektrochemicznej migracji jonów.
Obserwacje
Firma Zestron we współpracy z producentem urządzeń kolejowych, przetestowała w ten sposób trzy różne układy. Płytki zostały zmontowane przy użyciu stopu lutowniczego Sn62Pb36Ag2, a następnie pokryte zanurzeniowo lakierem silikonowym. Wizualna inspekcja była wykonywana przy użyciu spektroskopu UV (260 nm). W eksperymencie zaobserwowano w odniesieniu do pokrycia, częściowe pokrycie powłoką ochronną złącza, niewielkie rozwarstwienie na krawędziach i komponentach oraz korozję pomiędzy nóżkami złącza.
Badanie z powodzeniem pokazało potencjalne ryzyko korozji indukowane przez prądy upływu. Pełny 10-godzinny test był w stanie całkowicie zasymulować całkowity czas życia produktu założony przez producenta. Ponadto stwierdzono, że wpływ kwasu siarkowego oraz innych toksycznych gazów jest nieistotny w odniesieniu do produktów, które są stosowane w przemyśle samochodowym i kolejowym. Gazy te mogą głównie prowadzić do uszkodzeń, gdy urządzenie jest bezpośrednio narażone na działanie wilgoci. Zatem właściwości ochronne powłoki mają bardzo duże znaczenie.
Z zastosowanego badania wynikają trzy wnioski dotyczące powłoki ochronnej: jakość badanej powłoki była generalnie wystarczająca, nawet podczas poddania produktu na działanie środowiska siarkowego. Uszkodzenia powodowane przez środowisko „normalne” i siarkowe są zbliżone, konieczne jest poprawienie jakości w okolicach złączy.
Wady wynikające z procesu starzenia się produktu nie są wykrywalne przy użyciu tej metody, jednakże razem z tą metodą badania powłoki ochronnej można używać inne powszechnie znane sposoby np. polegające na poddaniu urządzenia działaniu zmiennych temperatur.
Jeżeli chodzi o testy temperaturowe wyróżniamy dwa główne sposoby badania z powolną i gwałtowną zmianą. Obydwa testy wykonuje się w komorach klimatycznych. Druga metoda jest częściej stosowana i wydaje się ciekawsza. Próbka wkładana jest do urządzenia, które wyposażone jest w dwie komory o znacznie różnych temperaturach. Transport próbki odbywa się przy użyciu transportera. Czas przebywania próbki w obydwu komorach może być dowolnie ustawiany, tak samo jak czas przenoszenia płytki pomiędzy komorami.
Wnioski
Zademonstrowany w artykule przykład pokazuje, że zaproponowana metoda badania jest skuteczna i tania oraz pozwala zoptymalizować i skrócić fazę projektowania. W nisko zaawansowanych urządzeniach powłoki ochronne nakładane są z pominięciem mycia. Jednakże dla zaawansowanych aplikacji, aby uniknąć rozwarstwienia i zapewnić odpowiednią adhezję jest ono konieczne. Różne rodzaje zanieczyszczeń, które powstają w trakcie procesu lutowania mogą osłabić połączenie pomiędzy powłoką ochronną i powierzchnią. Mogą być one w łatwy sposób usuwane w trakcie procesu mycia. W odniesieniu do pełnego procesu produkcji NoClean, pełne mycie końcowego produktu znacząco wydłuża żywotność końcowego produktu. Z tych powodów od pewnego czasu obserwujemy znaczący wzrost zainteresowania procesami mycia i poszukiwania optymalnego i stabilnego procesu.
Artykuł firmy Zestron tłum. Jakub Opałka
PB Technik
www.pbtechnik.com.pl