Elektronik 05/2015 - Systemy magazynowania komponentów
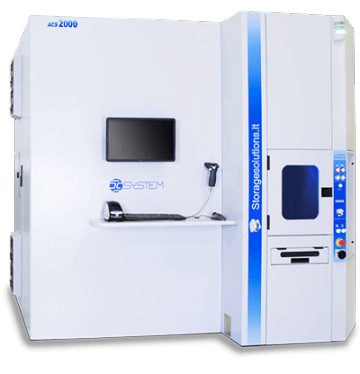
Produkcja masowa wymaga utrzymania magazynu komponentów, który zapewni przestrzeń i odpowiednie warunki składowania dla nich. Czy fabryki mogą sobie pozwolić na budowanie ogromnych magazynów? Czy może jest alternatywne rozwiązanie dla takich potrzeb? Odpowiedź w poniższym artykule.
Nowoczesne systemy zarządzania i magazynowania dla komponentów SMD
Technologia montażu powierzchniowego SMT dzięki możliwości pełnej automatyzacji, łatwość i elastyczność procesu produkcji pozwala na maksymalizację korzyści ekonomicznych i jakościowych dla producentów elektroniki. Chęć uzyskania jak największej wydajności linii produkcyjnych oraz wysokie wymagania techniczne stawiane gotowym urządzeniom powodują, że producenci muszą jak najlepiej optymalizować proces SMT. Jednym z ważniejszych wymogów jest zapewnienie optymalnych warunków przechowywania wrażliwych komponentów SMD oraz odpowiednie zarządzanie magazynem tak, aby przestoje linii produkcyjnych były jak najkrótsze.
Na rynku są dostępne dedykowane rozwiązania pozwalające na eliminację większości problemów wiążących się z przechowywaniem podzespołów.
Pierwszym istotnym problemem w magazynowaniu podzespołów jest wpływ wilgoci zawartej w powietrzu. O negatywnych skutkach oddziaływania tego czynnika nikogo nie trzeba przekonywać. Obudowy komponentów SMD są podatne na absorpcję wilgoci z otaczającego je powietrza. W wyniku dyfuzji wilgoć wnika w strukturę elementów, gromadząc się w ich wnętrzu. Podczas procesu lutowania rozpływowego, pod wpływem wzrostu temperatury, zmagazynowana wilgoć gwałtownie zwiększa swoją objętość, powodując mikropęknięcia. Problemem jest też postępująca korozja i inne uszkodzenia, gdyż są one niewidoczne dla standardowych systemów inspekcji. Negatywny wpływ wilgoci jest tym większy, im wyższą temperaturę osiągają komponenty podczas lutowania. W zawiązku z powyższym technologia bezołowiowa czyni montowane elementy jeszcze bardziej narażonymi na defekty tego typu.
W zależności od typu i materiałów użytych podczas produkcji obudowy, komponenty są w różnym stopniu podatne na absorpcję wilgoci oraz na uszkodzenia podczas lutowania rozpływowego. Poziomy wrażliwości na wilgoć komponentów MSD (Moisture Sensitive Devices) zostały określone w normie IPC/JEDEC J-STD-020D.1. Jak pokazano w tabeli 1, komponenty mają określony przez producenta poziom wrażliwości na wilgoć i co za tym idzie przypisany maksymalny czas, przez który mogą przebywać poza środowiskiem suchym (<5% RH). Wymusza to na producentach kontrolę czasu spędzanego przez dany komponent poza suchym opakowaniem próżniowym lub szafą klimatyczną.
Rozwiązania firmy Essegi
Na rynku dostępne są różne systemy przeznaczone do przechowywania komponentów MSD, od najprostszych opakowań próżniowych (dry bag) po zaawansowane szafy klimatyczne. Omówienie charakterystycznych funkcjonalności tych produktów warto dokonać na przykładzie sprzętu produkowanego przez włoską firmę Essegi, która specjalizuje się w produkcji nowoczesnych rozwiązań magazynowych do przechowywania wrażliwych komponentów. Urządzenia te oprócz utrzymywania i kontroli wilgoci na wymaganie niskim poziomie (<5% RH) automatycznie zliczają i kontrolują czas przez który komponenty wrażliwe znajdują się poza magazynem. Czas ten jest porównywany z wartościami dopuszczalnymi. Gdy limit czasu zostanie przekroczony urządzenie komunikuje to oraz blokuje dane opakowanie z komponentami przed użyciem w produkcji.
Opakowania z elementami są umieszczane w specjalnych kasetach, w których są pobierane oraz podawane automatycznie przez urządzenie. Dzięki zastosowaniu kaset w magazynie można przechowywać wszystkie rodzaje opakowań, które się w nich mieszczą, a więc rolki, tacki JEDEC, worki, końcówki taśm. Operacja załadunku/rozładunku odbywa się przez specjalne okienko zlokalizowane na froncie maszyny, dzięki czemu istnieje możliwość jednoczesnego podania lub pobrania do 27 kaset z rolkami na taśmy szerokości 8 mm. Takie rozwiązanie powoduje, że podczas załadunku/rozładunki wpływ wilgoci z zewnątrz na wewnętrzną atmosferę magazynu jest minimalny.
Każde opakowanie umieszczone w magazynie jest opatrzone kodem kreskowym, który maszyna automatycznie skanuje. Oprogramowanie zawiera bazę danych o komponentach. Przechowywane są tam informacje o typie magazynowanych komponentów, liczbie w danym opakowaniu, stopniu wrażliwości na MSD itd.
Dzięki automatycznemu przypisywaniu pierwszego wolnego miejsca w magazynie do wprowadzanego opakowania komponentów, wyeliminowany został problem istnienia pustych przestrzeni magazynowych występujący w standardowych magazynach. Pozwala to na redukcję potrzebnego miejsca o około 70% w stosunku do standardowych rozwiązań.
Połączenie magazynu z automatem Pick & Place lub innym zewnętrznym systemem produkcyjnym pozwala na automatyczne przesłanie informacji o aktualnie potrzebnych komponentach i ich ilości oraz podanie ich przez urządzenie. Dzięki temu załadunek i rozładunek magazynu nie zabiera czasu operatora oraz eliminuje możliwość pobrania błędnego opakowania. Ponadto baza danych o komponentach pozwala na bieżącą kontrolę stanów magazynowych. Oprogramowanie firmy ESSEGI sygnalizuje, gdy ilość któregoś ze zmagazynowanych elementów spada poniżej określonego poziomu, co pozwala na przygotowanie zakupów. Powyższe cechy pozwalają na redukcję czasu przestojów linii produkcyjnej SMT nawet o 80%.
Skrócenie przestojów przekłada się na znaczne zwiększenie wydajności, co daje wymierne oszczędności. Przy założeniu półgodzinnego przestoju linii produkcyjnej w ciągu jednej zmiany, spowodowanego brakiem potrzebnych materiałów, kosztu godzinnego przestoju linii na poziomie 1 tys. złotych oraz 240 dni roboczych w ciągu roku, oszczędności związane z zastosowaniem systemu ESSEGI to blisko 100 tys. złotych rocznie. Powyższe kalkulacje nie uwzględniają oszczędności związanych z redukcją niezbędnego miejsca magazynowego oraz skróceniem czasu pracy operatora.
Możliwość połączenie wielu urządzeń w jeden system pozwala otrzymać magazyn o pojemności przystosowanej do potrzeb produkcji. Magazyny są dostępne w dwóch wersjach w pełni automatycznych ACS2000 (pojemność do 2059 taśm 8 mm) i ACS1100 (pojemność do 1100 taśm 8 mm) oraz dwóch w postaci szaf z półkami ACS500 oraz ACS400.
PB Technik
www.pbtechnik.com.pl