Elektronik 04/2018 - Bezdotykowa liczarka komponentów X-Ray
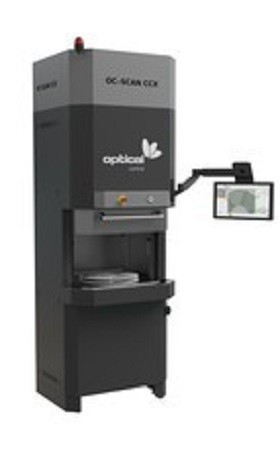
System CCX firmy Optical Contol zapoczątkował erę zmian w zakresie magazynowania komponentów SMD skracając i uproszczając do minimum proces ich zliczania.
Bezdotykowa liczarka komponentów X-Ray
System CCX firmy Optical Contol zapoczątkował erę zmian w zakresie magazynowania komponentów SMD skracając i uproszczając do minimum proces ich zliczania. Patrząc na jego możliwości można powiedzieć, że szybko stanie się standardowym wyposażeniem nowoczesnej hali produkcyjnej oraz przepustką do Industry 4.0. Pomysł na konstrukcję automatycznej liczarki bazującej na aparacie rentgenowskim powstał w firmie Elektron Systeme, zajmującą się usługami montażu elektroniki oraz produkcją własnych wyrobów. Przy szerokim spektrum produktów, była ona zmuszona codziennie przeprowadzać inwentaryzację stanu komponentów SMD w magazynie. Z jednej strony duża liczba podzespołów zapewniała ciągłość pracy linii SMT, ale z drugiej strony stwarzała problemy z logistyką, kontrolą zużycia oraz rozliczaniem wg faktycznego stanu. Uzyskanie tych danych wymagało od personelu dużo wysiłku, chociażby ze względu na standardowe dla pracy linii odrzuty komponentów i konieczność liczenia przed oraz po produkcji. Z takich powodów firma postawiła na budowę systemu zliczania komponentów w rolkach przy użyciu technik rentgenowskich. Dla takiej niewielkiej firmy jak Elektron Systeme, był to gigantyczny wysiłek.
Jednym z największych problemów do opanowania było duże zróżnicowanie wykorzystywanych komponentów SMD, od małych rezystorów typu chip o długości 200 μm aż do dużych kilkucentymetrowych złączy. Niezależnie od kształtu i geometrii wszystkie muszą zostać zliczone bez zmiany platformy sprzętowej urządzenie z jednakową dokładnością i dużą prędkością. Drugi problem dotyczył wymaganego dużego pola operacyjnego – do 50×50 cm, co zmusiło do budowy specjalnej kamery o rozdzielczości 13 megapikseli, aby możliwe było uchwycenie wszystkich szczegółów. Obrazy są poddawane obróbce przez wydajne algorytmy wewnętrznego oprogramowania OC-Scan CCX liczące elementy na obrazie w kilka sekund.
Przemysł 4.0
Automatyczne i szybkie liczenie elementów to niższe koszty magazynowania, logistyki, zaopatrzenia, lepsze wykorzystanie zasobów i niższe koszty pracy. Wykorzystując możliwości urządzenia CCX, można też sprawdzić bez konieczności otwierania rolki, które pozostają nadal szczelnie zamknięte np. w próżniowym opakowaniu, co jest kluczowe dla zapewnienia wysokiej jakości w produkcji.
Najważniejsze kryterium przemawiające za taką inwestycją w skaner Optical Control to właśnie oszczędność czasu. Ręczne załadowanie oraz policzenie komponentów klasyczną liczarką zajmuje około 5 minut, dla urządzenia X-Ray, analogiczna czynność zajmuje mniej niż 10 s. Można powiedzieć, że otrzymujemy oszczędność czasu na poziomie 98%. Dodatkową korzyścią jest wysoka dokładność liczenia przekraczająca 99,9%. Automat się po prostu nie myli, a człowiek niestety przy żmudnych i powtarzalnych zadaniach niestety tak.
Drugim argumentem przemawiającym za każdą inwestycją jest czas zwrotu z inwestycji. Posłużmy się tutaj przykładem osoby, przed którą stoi zadanie sprawdzenia 600 rolek komponentów dziennie. W takim przypadku porównanie wymaganego czasu to niecała godzina na korzyść CCX do trzydziestu trzech godzin. Są to oszczędności idące w tysiącach złotych każdego miesiąca! Nic dziwnego, że remanent jest jednym najmniej lubianych dni w roku dla każdej firmy. Wynika to z konieczności przeliczenia każdej pozycji w systemie, niejednokrotnie po kilka razy z powodu różnic wynikających z planowanych zużyć a faktycznych rozliczeń. Skaner CCX jest rozwiązaniem akceptowanym przez każdego audytora jako urządzenie rzetelne od strony prawnej, które może posłużyć do rozliczania magazynu w celach podatkowych.
Na koniec, warto wspomnieć o podwyższeniu wydajności produkcji wynikającej z świadomości faktycznie posiadanej liczby komponentów. Taka wiedza jest nieoceniona w przypadku planowania przezbrojeń, kolejnych zakupów oraz oceny zużycia w przeszłości. Taka precyzyjna informacja jest podstawą działania firmy w czasach Industry 4.0.
Opisywane problemy i korzyści płynące z zastosowania skanera rentgenowskiego CCX w największym stopniu dotyczą wszystkich firm EMS oraz zleceniobiorców projektów sektora wojskowego oraz medycznego, gdzie nieduże wolumeny produkcyjne oraz duże zróżnicowanie produktowe oraz ogólna złożoność projektów przekładająca się na dużą liczbę różnorodnych podzespołów na płytkach drukowanych, wymuszają niezliczone przezbrojenia linii produkcyjnej, a co za tym idzie przeliczenie czasem po 500–600 rolek. W takich przypadkach korzyści z zastosowania CCX są jeszcze wyższe.
Rozwój nie zna granic
System OC-Scan CCX jest dostępny na rynku zaledwie od 3 lat, ale już teraz firma Optical Control razem z Elektron Systeme wprowadzają na rynek kolejną 3. generację tego sprzętu. Okazuje się, że bliska współpraca z siostrzaną firmą EMS powoduje ciągłą ewaluację nowych pomysłów, rozbudowę istniejących oraz udoskonalanie konstrukcji pod względem ergonomicznym. Tak bliska współpraca skraca czas potrzebny do wprowadzenia zmian, dzięki czemu są one wprowadzone niemal natychmiast, a po testach dostępne dla wszystkich.
Nowa generacja skanera o oznaczeniu CCX.3 jest znacząco mniejsza od poprzedników, co pozwala na transport bez konieczności angażowania zewnętrznej firmy przewozowej. Można ją też przenieść przez większość drzwi, a na hali produkcyjnej bądź magazynowej zajmuje powierzchnię mniejszą niż 0,64 m2. Konstrukcja została też poprawiona od strony ergonomii, w celu umożliwienia jej obsługi w pozycji siedzącej lub stojącej.
Znaczące ulepszenia w oprogramowaniu skanera doprowadziły do zwiększenia precyzji liczenia komponentów 0201 i skrócenia czasu. Nowa wersja jest w stanie zliczyć komponenty w czterech 7-calowych rolkach w czasie poniżej 20 s. Zalety skanera doceniła Hella – wiodący producent innowacyjnego oświetlenia oraz elektroniki motoryzacyjnej. Korzyści pracownicy firmy widzą szczególnie przy produkcji prototypów, w których stosuje się wiele rożnych rodzajów komponentów. Prosta obsługa maszyny oraz zwiększone możliwości, znacząco ułatwiają pracę i w naturalny sposób zmniejszają koszty. Sprawdzając otrzymany towar, nieprawidłowości mogą zostać wykryte natychmiast, bez rozpakowania i uwzględnione w systemie. Takie dodatkowa inspekcja dostaw, wyraźnie podniosła skuteczność planowania przed rozpoczęciem produkcji.
Traceability
Realizując zlecenie jesteśmy w stanie przeliczyć w krótkim czasie rolki niezbędne do produkcji, a następnie po jej zakończeniu zliczyć je ponownie, otrzymując faktyczną zużytą ilość podzespołów, którą dzięki oprogramowaniu możemy powiązać z dokumentacją zlecenia. Naturalnie, nowy CCX gwarantuje również pełne traceability dla każdej rolki. Dane o wykorzystaniu każdej z rolek mogą być odtworzone w przedziale miesięcy, a nawet lat, co jest szczególnie istotne dla klientów z sektora motoryzacji.
Gotowy od 1 sekundy
Wszystkie wersje skanera CCX są dostarczane wraz z biblioteką komponentów, która umożliwia pracę urządzenia natychmiast po instalacji. Nawet jeśli komponent nie znajduje się w bibliotece, istnieje prosty tryb nauczania, w którym algorytm rozpoznawania jest dobierany i sugerowany użytkownikowi. W CCX.3 obywa się to całkowicie automatycznie – bez szczegółowej wiedzy na temat komponentu. Nowe oprogramowanie CCX.3 mierzy wymiary komponentów na podstawie obrazu z kamery rentgenowskiej i automatycznie dobiera parametry dla procedury liczenia. Wszystko trwa kilka sekund.
Ocena wiarygodności
Zawarty w oprogramowaniu moduł oceny wiarygodności wykonuje analizę statystyczną liczenia i ocenia dokładność oraz jakość wyniku, która może się różnić w zależności od jakości zdjęcia i ułożenia przedmiotu. Dla użytkownika wynik jest oznaczany poprzez podświetlenie konkretnych wyników testu na czerwono, żółto oraz zielono. Wyniki oznaczone innym kolorem niż zielony muszą być ocenione przez operatora lub ew. powtórzone.
Ponadnormatywne komponenty
Duże komponenty produkowane w rolkach są szczególnie uciążliwe w liczeniu, ponieważ ich rozmiar powoduje zanikanie przerw pomiędzy kolejnymi rzędami, powodując nakładanie się znalezionych komponentów na siebie. Jest to sytuacja nieunikniona, dlatego oprogramowanie zostało specjalnie zoptymalizowane w celu rozwiązania takiego problemu oferując stałą jakość niezależnie od kształtu czy rozmiaru komponentu.
Drypack
Podzespoły stosowane w sektorze wojskowym lub medycznym są szczególnie wrażliwe na wilgotność. W takich wypadkach stosowane jest specjalne opakowania podczas dostawy wyposażone w tzw. drypack, który przeważnie przyklejony jest bezpośrednio do rolki. Jest to kolejna z niespodziewanych sytuacji, która może w znaczącym stopniu zakłócić pomiar rentgenowski. Specjalny moduł w oprogramowaniu Optical Control pozwala bezbłędnie rozpoznać takie dodatki i zastosować dodatkowe filtry mające na celu wyeliminowania go na czas pomiaru. Funkcja działa prawidłowo niezależnie od tego, czy drypack znajduje się na komponentach, czy też obok.
Jakub Karpowicz
j.karpowicz@pbtechnik.com.pl
tel. kom. 697 709 697
www.pbtechnik.com.pl