Elektronik 12/2019 - Traceability w produkcji elektroniki
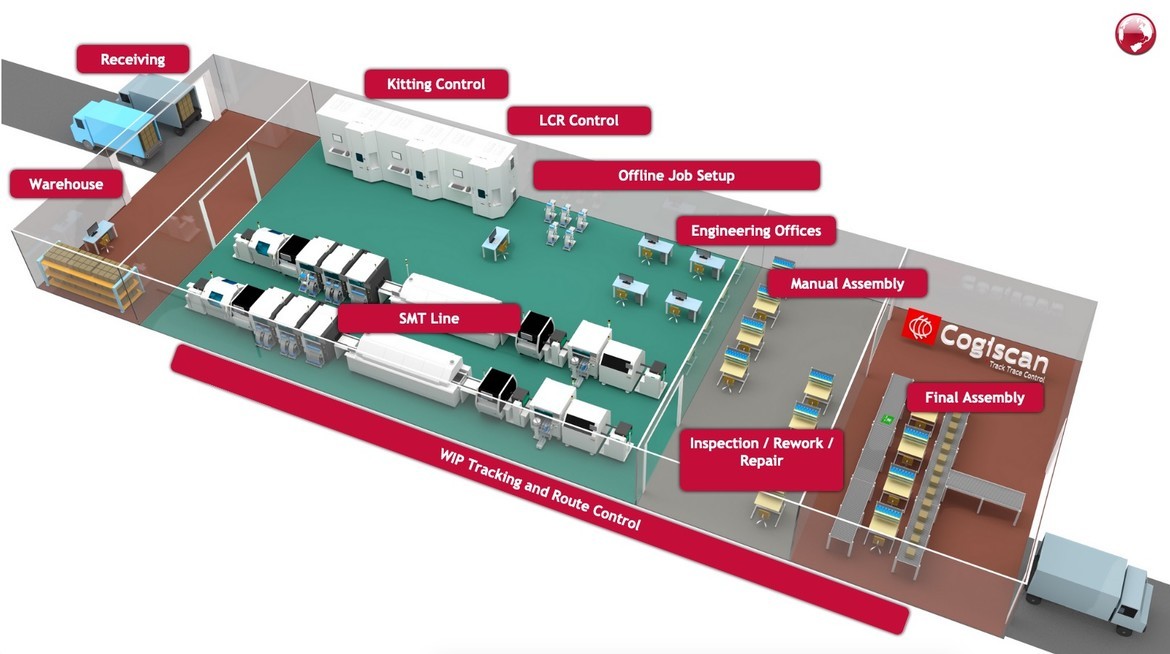
Jakie są zadania i możliwości systemów traceability w produkcji elektronicznej?
Traceability w produkcji elektroniki
W ostatnich latach traceability stało się pojęciem dość popularnym i zapewne każdy przynajmniej raz się z nim zetknął. Duzi producenci elektroniki chwalą się, że mają system traceability, niektórzy zleceniodawcy pytają podwykonawców o posiadanie takiego systemu. Z tego powodu prawie każdy producent ma wdrożenie takiego systemu w planach na przyszłość jako „coś co warto mieć”. Czy jednak wiemy co to naprawdę jest? I czy naprawdę „warto to mieć”?
Zacznijmy od pytania drugiego: „czy warto”? Na rynku istnieje tyle rozwiązań, że niemożliwe jest odpowiedzenie na to pytanie wprost. Wszystko zależy od tego, jaki system wdrożymy i co chcemy za jego pomocą osiągnąć.
Niektóre systemy są bardzo rozbudowane i oprócz zwykłej rejestracji w bazie danych integrują się z procesem produkcyjnym oferując „wartość dodaną” w postaci kontroli procesu produkcyjnego i zapewnienia jakości. Inne są po prostu bazą danych wymagającą obsługi i utrzymania, i fakt ich posiadania może być argumentem dla zleceniodawcy, ale nie wnoszą nic do procesu produkcji, a nawet stanowią dodatkowe obciążenie. Jak widać „warto” pod warunkiem, że dopasuje się system do swoich potrzeb.
A więc czym jest Traceability?
Słowo „trace” w języku angielskim oznacza śledzenie. I w największym skrócie system traceability umożliwia „prześledzenie” procesu produkcji danego wyrobu. Aby było ono możliwe, automatycznie wiąże się z wprowadzeniem identyfikacji.
Już na tym etapie można zauważyć duże pole do zróżnicowania komplikacji i złożoności systemu. Jak dokładna ma być identyfikacja? Chcemy identyfikować partię produkcyjną czy każdą sztukę wyrobu? Identyfikacja każdej sztuki umożliwia w razie ewentualnych reklamacji, „cofnięcie się w czasie” i prześledzenie procesu produkcji tego konkretnego egzemplarza. W razie, gdyby pojawiało się więcej problemów z danym wyrobem można je ze sobą powiązać i wyciągnąć wnioski. Identyfikacja na poziomie partii produkcyjnej kończy się w momencie przekazania wyrobu kontrahentowi. Jeżeli później wrócą do nas jakieś egzemplarze jako reklamacja, to skąd będziemy wiedzieli z której są partii produkcyjnej? Poza tym w ramach produkcji jednej partii warunki też się zmieniają (operatorzy maszyn, materiały użyte do produkcji itp.) i trudno jest wykorzystać zgromadzone dane do wyciągnięcia jakichś wniosków, które pomogłyby wyeliminować problem. Jak widać, aby dane były jak najbardziej użyteczne, muszą być bardzo dokładne. Wiąże się to nie tylko z rejestracją i identyfikacją samego wyrobu, ale również materiałów, komponentów, urządzeń, operatorów maszyn itp.
Co to oznacza dla organizacji produkcji?
Jeżeli traceability ma być pełne i użyteczne, oznacza to, że jego wprowadzenie wiąże się z koniecznością przeorganizowania wielu rzeczy jeszcze na etapie wdrożenia, a często nawet przed. Dlaczego? Najlepiej pokaże to przykład obrazujący to, co chcemy osiągnąć i jakie informacje uzyskać z systemu traceability.
Załóżmy, że w procesie reklamacyjnym stwierdziliśmy, że problem występujący w naszym wyrobie dotyczy wadliwego elementu na PCB. Natychmiast rodzi się pytanie: na ilu i na których płytkach został zamontowany ten element? Aby taką zależność dało się uzyskać, konieczne jest nadanie każdej płytce unikalnego numeru seryjnego. Wynika to z prostej zależności. Przy produkcji dłuższych partii operatorzy wymieniają rolki z elementami na maszynach. Bez numerów seryjnych PCB, jeżeli stwierdzimy, że dany (wadliwy) element został zamontowany w trakcie produkcji zlecenia, to w przypadku braku numerów seryjnych na płytkach nie będziemy mieli pewności, na które trafił ten konkretny komponent i będziemy musieli sprawdzić lub naprawić całą partię. A co, jeżeli dana rolka była użyta częściowo pod koniec produkcji jednej partii płytek a skończyła się dopiero w trakcie kolejnego zlecenia?
Wniosek 1: do dobrego traceability konieczna jest serializacja produkcji (numery seryjne wyrobów).
Wracając do naszej sytuacji z reklamowanym wyrobem. Mamy płytkę, na której ewidentnie jakiś komponent wygląda na wadliwy i jest podejrzenie, że zamontowaliśmy wadliwą partię elementów na płytkach PCB.
Niektóre automaty dopuszczają sytuację, że mamy założone kilka rolek takiego samego elementu na raz, bądź to na jednej maszynie, bądź na kilku maszynach w linii. Rodzi to następujące pytania: Jaką mamy pewność czy w danym momencie mieliśmy założone rolki z tej samej dostawy lub partii? Jeżeli wykryliśmy wadliwy element, to ile jeszcze rolek z tej partii zostało zamontowanych (również w innych zleceniach)? Jeżeli na maszynach były rolki tego samego elementu, ale z różnych partii i tylko jednej z nich dotyczy problem, to które konkretnie lokacje są OK, a które nie?
Wniosek 2: Do prawidłowego śledzenia na tym poziomie, każda rolka elementu musi być identyfikowalna w systemie. Oznacza to, że każda rolka musi posiadać unikalny numer (identyfikator). Jeżeli dodatkowo chcemy, aby dane z systemu traceability były zgodne na przykład z systemem ERP może to wymagać zmiany sposobu postępowania również w systemie ERP.
Zagadnień do analizy jest więcej
Jeżeli dział zakupów kupuje większą partę danego elementu (co przekłada się fizycznie na wiele rolek) to jak te dane są wprowadzane do ERP? Jeżeli jedną pozycją to, aby dało się pracować z traceability, trzeba by je od nowa wprowadzać ręcznie, rolka po rolce do tego systemu. Utrudniłoby to również synchronizację i wymianę danych między tymi systemami.
Dodatkowo, jeżeli nawet jesteśmy w stanie wyciągnąć z systemu traceability listę wszystkich numerów seryjnych PCB których problem dotyczy, to gdzie one są w tej chwili? Czy wciąż są na linii produkcyjnej, w magazynie, czy zostały wysłane do odbiorców, a jeśli tak, to do których?
Wniosek 3: Wdrożenie traceability wiąże się bardzo często ze zmianą postępowania w innych systemach zarządzania firmą (ERP, obsługa zakupów, sprzedaży itp.)
Podsumowując: Jeszcze na etapie przygotowawczym do wdrożenia traceability trzeba bardzo dobrze przemyśleć sposób postępowania z materiałem (elementami) na produkcji. Sposobem ich wprowadzania do systemu, śledzeniem w procesie sprzedaży gotowych wyrobów itp.
Konieczna jest ponadto analiza procesu produkcji
Osobnym zagadnieniem jest sposób potraktowania procesu produkcji. Jak szczegółowo chcemy go analizować? Każdy proces produkcji możemy zdefiniować jako ciąg czynności, które wykonujemy na danym wyrobie, przy użyciu urządzeń i pracowników którzy je obsługują, a także materiałów, które są dodawane do wyrobu w trakcie tego procesu.
Im bardziej szczegółowo potraktujemy proces, tym więcej użytecznych informacji zgromadzimy. Możemy jako operację potraktować cały proces montażu powierzchniowego, ale również możemy analizować go na poziomie maszyn, traktując każdy automat SMD jako osobną operację.
Łatwo zauważyć, że im dokładniejszy i bardziej rozbudowany system traceability chcemy mieć, tym więcej informacji musimy w nim zgromadzić. Jednak równocześnie im więcej informacji będzie taki system zawierał tym bardziej będzie użyteczny.
Jednak informacje te trzeba jakoś gromadzić i im będzie ich więcej tym większy nakład pracy będzie potrzebny do obsługi całego systemu. Oznacza to zwiększenie kosztów produkcji, a przecież tego nikt nie chce.
Co zatem wybrać?
Zależy to od konstrukcji i funkcjonalności wdrażanego systemu. Możliwe jest zbieranie nawet bardzo szczegółowych informacji przy minimalnym zaangażowaniu pracowników.
Na rynku działa wiele firm oferujących systemy traceability. Niektóre z nich są firmami czysto software'owymi oferujące wielostanowiskowe bazy danych do gromadzenia potrzebnych informacji. Przy czym rozwiązanie opierające się wyłącznie na oprogramowaniu będzie wymagało wprowadzania danych „ręcznie” co albo utrudni pracę z tym systemem, albo zmusi do jego uproszczenia w celu osiągnięcia kompromisu pomiędzy niezbędnym nakładem pracy, a szczegółowością zbieranych danych.
Oczywiście niektórzy dostawcy wprowadzają usprawnienia takie jak na przykład czytniki kodów kreskowych w celu zminimalizowania operacji ręcznych, jednak całkowicie to ich nie eliminuje. Jedynie połączone rozwiązanie, gdzie oprogramowanie zintegrowane jest z dedykowanym oprzyrządowaniem zamontowanym na linii produkcyjnej umożliwia zbieranie tak dokładnych informacji, jak tylko sobie zażyczymy, przy minimalnym zaangażowaniu obsługi.
Jeżeli rozpatrzymy całą linię SMD jako operację produkcyjną to przy pomocy skanerów kodów kreskowych możemy dość prosto wprowadzić do systemu informacje o operatorze obsługującym linię, elementach zamontowanych w podajnikach oraz skanować produkt na wejściu/wyjściu procesu. Jednak w trakcie montażu uzupełniamy rolki z elementami. Jeżeli później okaże się, że któryś komponent był wadliwy, to wiemy tylko w której partii produkcyjnej był zamontowany. Określenie dokładnie na których płytkach występuje możliwe jest tylko w przybliżeniu, zwłaszcza jeśli linia składa się z dwóch lub więcej automatów a skanowanie płytek odbywa się tylko na wejściu/wyjściu linii. Nie mówiąc już o określeniu na których pozycjach znajduje się dany element, gdyż w niektórych automatach może być założona więcej niż jedna rolka tego samego elementu.
Wniosek 4: Nie da się wprowadzić dokładnego systemu traceability bez komunikacji z maszynami i ich oprogramowaniem.
I tutaj rodzi się następny problem. Na produkcji bardzo często mamy do czynienia z maszynami, wyprodukowanymi przez różnych producentów. Firma dostarczająca system traceability musi być w stanie skomunikować się ze wszystkimi maszynami, które posiadamy. Nie da się tego zrealizować konfigurując system funkcjonujący „obok” istniejącej produkcji. Na dodatek najlepiej, aby taka komunikacja była dwustronna i nie opierała się tylko na odczycie parametrów i danych z maszyny. Jeżeli wiemy już, że na produkcji jest „coś nie tak” to co z tego, jeżeli system nie będzie w stanie zatrzymać maszyny, która aktualnie produkuje wadliwe wyroby? Albo gdy już wiemy, że mamy partię wadliwych wyrobów na linii produkcyjnej, czy jesteśmy w stanie nie dopuścić tych wyrobów do następnego etapu?
Jeżeli nie, a wada jest nieusuwalna, to każda następna wykonana operacja stanowi dodatkowy koszt wycofania takiego wyrobu.
A co z dokumentacją procesów?
Powyższe rozważania dotyczą zaledwie zagadnienia związanego z „material traceability”, czyli śledzeniem materiałów (PCB, komponentów itp.) Mając już taki system, z taką ilością zgromadzonych danych, warto zastanowić się nad systemem który zapewni również „process traceability” czyli monitorowanie i sterowanie kolejnością wykonywanych operacji w procesie produkcji wyrobu. Dodatkowo „process traceability” wiąże się ze zbieraniem informacji również ze stanowisk testowych, AOI, SPI itp.
Oczywiście każde z tych urządzeń zawiera oprogramowanie umożliwiające analizę wykrytych błędów oraz stanowiska naprawcze i tym podobne moduły oprogramowania. Ale do celów syntetycznych nie zawsze potrzebujemy tak dokładnych danych, zdjęć itp.
Integracja danych z takich urządzeń umożliwia zebranie w jednym raporcie wszystkich informacji związanych z procesem produkcji danego wyrobu bez konieczności przeszukiwania kilku baz danych. Poza tym na podstawie informacji o statusie wyrobu (OK / NG) możemy sterować kolejnymi etapami jego produkcji, na przykład nie dopuścić do kolejnej operacji wadliwego wyrobu. Bez takiego połączenia zawsze można sobie wyobrazić sytuację, że operator omyłkowo włoży wadliwy produkt do dobrych i bez takiego systemu kontrolnego będą na nim wykonywane dalsze operacje, co podnosi koszt złomowania.
Podsumowanie
Każdy producent, czy to automatów montażowych, czy innych maszyn do produkcji oferuje opcję traceability. Problem w tym, że taki system ogranicza się do maszyn oferowanych przez tego producenta. A co z montażem ręcznym? Poza tym, przy bardziej złożonej produkcji, ile baz danych trzeba będzie nadzorować i przeszukiwać, aby znaleźć potrzebne informacje?
Nasza firma współpracuje z firmą Cogiscan, która jest producentem oprogramowania specjalizowanego do traceability. Są oni znani z faktu, że posiadają interfejsy do bardzo wielu istniejących na rynku maszyn i potrafią je zintegrować w jeden system zapewniający zarówno material traceability, jak i process traceability obejmujący cały proces produkcji, od przyjęcia ma magazyn pustych płytek PCB i elementów, poprzez montaż SMD, THT, operacje ręczne i automatyczne, aż po końcowy montaż finalnego produktu.
Zajmujemy się tymi zagadnieniami od 2004 roku, kiedy to instalowaliśmy w Polsce pierwszy taki system.
Zapraszamy do współpracy wszystkich zainteresowanych wdrożeniem takiego systemu u siebie.
Grzegorz Andryszczak
Dyrektor Techniczny w firmie PB Technik Sp. z o.o.
ul. Zwoleńska 27, 04-761 Warszawa
tel. 615 83 44
info@pbtechnik.com.pl